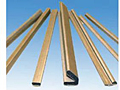
EMI & ESD Shielding Products
In sensitive applications such as medical electronics, mass transit systems, and vehicular control systems, electromagnetic interference (EMI) can have devastating consequences. Shielding products, therefore, must be able to provide reliable, long-lasting protection in order to prevent EMI from damaging and disrupting electrical devices and equipment.
Closely related to EMI is electrostatic discharge (ESD), a sudden flow of electricity between two charged objects caused by factors that may include a short or a breakdown. ESD grounding is necessary to prevent this discharge, which can have disastrous, life-threatening effects similar to those of EMI.
EMI Shielding Solutions
A wide range of EMI shielding solutions — which encompass ESD grounding solutions — are available to help ensure optimal reliability and safety; specific products, such as conductive elastomers for low closure force gasketing, as well as conductive tapes and laminates, can be integrated into electrical systems to provide protection. All of these solutions are quick and easy to implement.
EMI gaskets, flexible metal screens, wires, and foams all serve as effective seals to protect electrical systems from their surrounding environments. And unlike the metal sheets that were once used for EMI gaskets, modern-day gaskets resist deformation under the pressures of sealing and often include elastomers for enhanced shielding performance.
Conductive elastomers — fully cured silicones or fluorosilicones comprised of highly conductive particles — simultaneously provide EMI shielding and environmental sealing for dust and water. Conductive fillers ensure compatibility among electric currents and offer low contact resistance among various surfaces. Additionally, these elastomers remain in shape in demanding applications, allowing for longer lifespans and reduced costs. They’re also tear-resistant and often come with the option of adhesive backing, making for easy installation. Offering a wide range of benefits for manufacturers and system operators alike, conductive elastomers have become increasingly popular in EMI shielding applications.
EMI Tapes and Fabric Over Foam Solutions
At Robert McKeown Company, Inc. (RMC), we offer several lines of Parker Chomerics products, including fabric over foam (fof) EMI solutions and CHO-FOIL® tapes.
CHO-FOIL® tapes fall under the conductive tape and laminate category, offering a cost-effective EMI shielding and ESD grounding solution for a broad range of commercial applications. Available in the most popular shielding materials, including many variations of copper, aluminum, and nickel-plated fabric, these tapes also offer aesthetic benefits. The embossed version of CHO-FOIL® copper tape, in particular, provides a sleek, modern aesthetic. Strong yet lightweight, this tape is corrosion-resistant and engineered to be highly conductive while remaining sensitive to pressure. These characteristics enhance its shielding performance and make it ideal for most EMI shielding and grounding applications.
Innovative fabric over foam products, meanwhile, provide reliable shielding from electromagnetic fields in the radio frequency spectrum that can severely harm electrical systems. Parker Chomerics’ fabric over foam products are constructed of either conductivity-plated fabric or wire mesh fitted over low closure urethane foam. Allowing for simple installation, these solutions have excellent compressibility, require fewer fasteners, and feature self-terminating gaskets.
Learn More
For more information on EMI shielding products and ESD grounding solutions, and to discuss how they can help protect your critical electrical systems, reach out to the expert team at Robert McKeown today.
/Asset/SOFT-SHIELD-3500-Low-Closure-Force-EMI-Strip-Gaskets.jpg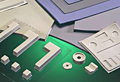
Thermal Interface Materials
Robert McKeown Company provides a range of high-quality, high-performance materials for electronics applications, including thermal interface materials (TIM). These materials are critical elements of thermal management systems. They facilitate the transfer of heat between two or more solid surfaces to prevent overheating and other excessive heat-related issues. They work by filling in the spaces between rough surfaces where small pockets of air can form and prevent heat from dissipating.
Types of Thermal Interface Materials
There are many types of thermal interface materials, each of which has unique characteristics that make it suitable for particular applications. The TIM products available at Robert McKeown are:
- Gap filling thermal interface: Gap filling thermal interface materials are engineered to deform gaps to resolve compliancy or flatness problems while ensuring efficient heat transfer. They absorb gaps without producing a large amount of stress.
- Thin interface thermal insulators: Thin interface thermal insulators have a highly thin form that still offers good thermal, electrical, and mechanical properties.
- Thermally conductive double-coated attachment tapes: Thermally conductive, double-coated attachment tapes serve as an easy to apply and use thermal management solutions.
- Phase change thermal interface: Phase change thermal interface materials are solid at room temperature and soften at operating temperature, which makes them easy to apply. They conform to surfaces with light pressure and are non-electrically conductive.
Applications for Thermal Interface Materials
Thermal interface materials are essential for thermal management in many industries. Typical applications include:
- Electronics packaging: As electronic assemblies become increasingly compact and processing bandwidth increases, thermal energy also escalates and becomes more challenging to manage. TIMs are key to resolving these issues; in electronics packaging, they facilitate heat transfer by improving contact between surfaces.
- Household appliances: Home appliances contain many heat-producing components that require effective and efficient thermal dissipation solutions to ensure long operating lives. TIMs are used to fill the gaps between these components and heat sinks to decrease internal temperatures.
- Lighting technology: LED lighting technology uses both electrically conductive and nonconductive TIMs to dissipate heat from system areas where excessive temperatures could lead to failure.
- Medical technology: Thermal interface materials are found in various electronic components and systems used for medical imaging and other medical electronics applications. Some examples of heat sources in medical electronics that require TIMs include microprocessors, power supplies, CT scanner components, surgical laser systems, DC-DC converters, and more.
- Industrial automation: Semiconductors are integral components of automation equipment. Since excessive heat can damage them, leading to reduced lifespan or unexpected failure, incorporating proper thermal management materials is vital.
Robert McKeown: A Leading Provider of Thermal Management Products
Many electronic devices and systems contain thermally sensitive components that are critical to their operation. Since these products naturally produce and gather heat during use, it is essential to establish and implement thermal management solutions to prevent excessive temperatures.
At Robert McKeown, we offer a broad selection of thermal interface materials that help resolve issues with overheating, ensuring the reliability and longevity of electronic products. Our experts can assist you in identifying and sourcing the ideal material for your application. To learn more about our products, contact us today. Request a quote to get started on your thermal interface material solution.
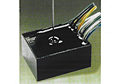
Electronics Potting & Encapsulation
No matter what the specific application or industry, protecting electronic components is crucial for ensuring long-lasting system durability and functionality. Available in various formats including encapsulates and gels, electronic potting compounds provide reliable protection for both complex and simple components in any type of environment.
Silicone encapsulates, in particular, contain no solvents or cure byproducts, allowing for lower costs. Providing optical clarity and thermal conductivity, they can perform in temperatures ranging from -45°C to 200°C. Silicone gels, on the other hand, provide ideal protection from moisture, as well as thermal and mechanical stress. They also protect against bubble or crack generation in high-voltage applications.
Some of the industry's top manufacturers offer several types of electronic potting compound materials to help minimize stress and maximize reliability for flexible and rigid print circuit boards (PCBs), LED lighting and displays, industrial equipment, high-voltage electrical components, and power modules, among many other devices and systems. Robert McKeown carries a wide range of Dow and Henkel Adhesive products; just a few of their many offerings are outlined below.
Dow Silicone Encapsulants
Used to protect circuitry from mechanical or thermal shock, vibration, chemical attack, humidity, and other stressors, Sylgard® silicone encapsulates from Dow provide unmatched electronics encapsulation.
Silicone encapsulates are available in two main types: condensation cure and addition cure, both of which can be supplied as one-part or two-part electronic potting compound systems to meet specific application needs.
One-part condensation cure silicones allow for ease of application and easy dispensing from a cartridge or tube, making these encapsulates ideal for thin-section cures of less than 7 millimeters. However, fixed cure speeds are required, and viscosity options are limited. Two-part condensation cure silicones, on the other hand, have a high tolerance to variations in the catalyst ratio and limited risk of inhibition. They do have slightly higher shrinkage levels than addition cures, however, as well as a reversion to liquid if heated in a container.
As with one-part condensation cure systems, one-part addition systems also allow for optimal ease of application. Featuring good physical strength, they can be used for both thin and thick section cures. However, they require heat to cure and have a short shelf life. Two-part addition cure systems allow for excellent deep section cures and low shrinkage rates. Their pot life can also be easily extended with an additive. Adequate adhesion is difficult to achieve with these two-part electronic potting compound systems, however, and they’re also prone to inhibition.
Henkel Loctite Epoxy Catalysts
Another ideal option for electronic potting applications, Loctite® epoxy catalysts from Henkel Adhesives offer excellent adhesion, high chemical resistance, and high-temperature physical properties. Epoxies are also extremely rigid and have a high tensile strength. And because most epoxies provide electrical insulation and have great moisture resistance, they’re ideal for outdoor use.
Two-Part Epoxy Compounds
Mix ratios are used for two-component epoxy systems to determine the amount of resin and epoxy catalyst needed for a full cure. The chemical makeup of the resin and the catalyst determine the mix ratios that must be followed; if not properly followed, various issues can occur, such as no cure or soft cure, as well as high exotherm during reaction, which can cause shrinkage.
Mix ratios are expressed by weight, volume, or PHR (parts per hundred). The ratio by weight and the ratio by volume are often different due to variations in density between resins and catalysts. Measurements by weight are more accurate, however, and are generally preferred over volumetric proportioning. When estimating the amount of mixed material, it’s important to know the pot life of the product in order to avoid wasting material.
Encapsulants & Potting Compounds from RMC
Robert McKeown Co., Inc., a family-owned fabricating distributor of engineered materials and electronic potting compounds, has been proudly serving clients for over 80 years. Our expert staff specializes in a wide range of protective solutions for electronics, and we work closely with all our clients to ensure products are tailored to their unique needs.
To learn more about Dow ’s electronic potting compounds and other adhesive products from manufacturers like Henkel, contact us or request a quote today.
/Asset/a1146.jpg
Adhesives & Sealants
Robert McKeown offers a variety of adhesive and sealant products for a wide range of commercial and industrial applications. Our silicone epoxy adhesives and sealants, in particular, are ideal for bonding, caulking, and sealing in electronics fabrication, facility maintenance, and construction applications.
Features and Uses of Electronics Sealants and Adhesives
Providing ultimate reliability and longevity, our electronics adhesives and sealants can be used to form bonds to many different surfaces and substrates, including ceramics, metals, glass, and filled plastics. These specialized solutions eliminate the need for mechanical fastening and clamping while allowing for optimal ease of processing. Reliable and efficient in temperatures ranging from -45 °C to 200 °C, our electronics adhesives and sealants provide excellent dielectric insulation.
Most silicone formulations are solventless, eliminating the need for special storage, ventilation, or handling. And because many of our electronics adhesives and solvents are reworkable, they offer great flexibility and allow for easier module repair.
Electronics adhesives and sealants are frequently used in automotive, communications, industrial, and energy industries, as well as consumer devices. Extremely versatile, these adhesives can be used for sealing lids and housing grooves, cushioning or stabilizing fragile components, affixing components such as capacitors and coils to circuit boards, adhering module lids and baseplates, and gasketing.
Silicone Adhesives
One of the most popular types of electronics adhesives, silicone adhesives provide excellent flexibility and high heat resistance, making them ideal for electrical, automotive, aerospace, and construction industries. There are several varieties of silicone adhesives available, including two-component systems that require a curing agent, one-component systems that cure through air moisture, UV or EB radiation curing adhesives, and pressure-sensitive versions that adhere to surfaces with little pressure.
RTV sealants (room-temperature vulcanizing) begin to cure as soon as they’re exposed to moisture in the air, so they must be used quickly. Pressure-sensitive sealants offer a permanent tackiness. UV- or radiation-cured sealants, on the other hand, require UV light to cure, while thermoset silicone sealants require heat to cure. Although not as strong as other sealants or adhesives, electrical silicone sealants remain flexible even when fully dried or cured. Various types of silicone sealants serve as ideal solutions for high-heat applications like engine gaskets.
In electronics fabrication, silicone adhesive sealants are often used for fixing parts on circuit boards, LCD module assembly, general sealing, and component protection. Specific formulations differ depending on intended use and can be customized to allow for enhanced thermal conductivity, superior protection of metal electrodes, and faster cure times. These sealants are available in chemical-, heat-, mildew-, and oil-resistant formulations to meet a wide range of application needs.
Industrial silicone epoxy is used for general-purpose fixture sealing of tubs, windows, ductwork, and gaskets, as well as general-purpose bonding and sealing.
Thermal Sealants
High temperatures often present problems for conventional adhesive materials and can affect printed circuit boards and assemblies. At Robert McKeown, we offer the highest-level special adhesive grades of thermal sealants, which allow for enhanced thermal conductivity. Both low-viscosity liquids and non-slump formations are available in two-cure chemistries.
We also offer one-part moisture-cure grades, which use room-temperature processing to cut back on equipment needs. After cure, the materials form strong but flexible bonds, which protect from mechanical stress and vibration. Both one- and two-part heat-cure solutions accelerate processing and support high throughput production.
Heat resistant silicone adhesives are extremely versatile materials and dispense easily at room temperature, but can also cure quickly at any thickness level at temperatures as low as 90°C. Efficacy and functionality are improved when higher temperatures accelerate cure times.
Chemical Resistant Adhesives
Chemical resistant silicone adhesives are commonly used in chemical processing plants, chemical piping and tanks, and medical devices. These adhesives can reliably protect against a wide range of chemicals and harsh materials, including acid, alcohol, and fuel. Depending on specific application requirements, they can also provide resistance against solvents, bases, sterilization, and water.
Epoxy Based Adhesives
Epoxy based adhesives are created by mixing a resin and a hardener. Curing is initiated when the resin is mixed with a certain catalyst. The covalent bonds resulting from this combination determine the rigidity and strength of the epoxy sealant.
Epoxy adhesives can reliably adhere to a variety of materials and are ideal for applications demanding chemical resistance, high strength, and low stress. Thermally conductive, microelectronic-grade, general-purpose, high-temperature and chemical resistant epoxy adhesives are available as both one- and two-part solutions. Epoxy adhesive and sealants allow for room temperature, thermal, or UV-curing capabilities.
Learn More
Robert McKeown Co., Inc. is proud to be a leading distributor of electronics adhesives and sealants for a wide range of applications. Family-owned and operated since 1937, we’re committed to constant innovation and improvement in everything we do. We offer a wide range of electronics adhesives and electronics sealants to meet all types of application needs; whether requiring flexible processing, simple assembly, strong adhesive performance, or thermal management, our clients are guaranteed top-quality, long-lasting products. Our expert staff works closely with customers to ensure solutions meet their unique requirements.
For more information on our electronics adhesives and sealants and to learn how they can help with your next project, request a quote today.
/Asset/a1019.jpg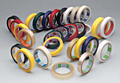
Electrically Conductive Tape & Composite Adhesives
Available in various formats and styles to meet specific requirements, electrically conductive tapes are essential for enhancing functionality and reliability in a wide range of applications. Some of the most popular types include electrically conductive adhesive tape and electrically conductive film, both of which provide reliable electronic isolation and ensure that direct electrical connection is not made between two or more circuits or their adjacent parts.
Electrically conductive tapes and films are used in many fields, including electrical, medical, and pharmaceutical, and can serve various purposes. Thanks to their durability in elevated temperatures, reliable electrical-contact capabilities without the need for pressure, and consistent adhesive capabilities, electronic tapes function well under even under significant environmental and mechanical stress.
Bonding of Composite Materials
Providing strength and reliability in critical applications, composite adhesive bonding helps engineers meet specific performance requirements. The process of bonding an array of similar or varied materials — such as fiber- and particle-reinforced thermosetting composites, carbon-matrix composites, metal alloys, polyester, titanium, glass, and rubber — composite bonding involves a matrix and a reinforcement; when combined, their different physical and chemical properties impart new properties, producing a single system. The most common composites are carbon fiber and glass fiber, as well as Kevlar and graphite-reinforced materials.
Adhesives for composite materials allow for optimal mechanical strength, protection against impacts and fractures, and provide mechanical and cryogenic shock resistance. These bonds also provide electrical insulation, allow for low shrinkage rates, and easily resist thermal cycling.
However, proper safety protocols must be followed to ensure long-term functionality of bonded parts. Environmental conditions, joint configuration, surface preparation, and adhesive properties must all be taken into consideration.
Adhesives Used in Composites Bonding
Because various applications require different types of bonding, there are a multitude of adhesives to choose from depending on the industry. Commonly used in the aerospace industry, composite adhesives are also used in automotive manufacturing, orthopedic devices, sporting equipment, and medical appliances.
Conductive film adhesives, electrically conductive tape, composite bonding tape, industrial nonstick fabrics, and heat sealing tapes are important in many composite bonding processes, as these materials provide insulation and resilience against harsh elements, thereby protecting consumers and manufacturers from fire hazards and shock risks. In production and manufacturing processes, these tapes and films can mask or hold parts in order to protect them from damage, and can also provide electrical conductivity across or between adhesive bonds.
Depending on the specific materials that will be bonded, several factors should be taken into consideration when choosing a structural adhesive for composite bonding purposes. Environmental factors like humidity and UV exposure must be kept in mind, as well as any potential mechanical challenges such as impacts and vibration. It’s also important to consider resistance to various chemicals, such as jet fuel or motor oil.
Electrically Conductive Tapes & Composite Adhesives from RMC
Robert McKeown Co., Inc. is proud to specialize in electrically conductive tapes for electronics applications. Family-owned and operated since 1937, our team remains committed to quality and innovation in everything we do, and our expert team works closely with clients to ensure they receive top-quality solutions tailored to their specific needs. Whether you require next-day availability, fast-track quotes, express samples, or next-day prototypes, we can provide a solution. To learn how our electronic tapes and adhesives can help with your next project, or to discuss the benefits of composite bonding with an expert, reach out to the team today. /Asset/a1167.jpgRobert McKeown offers a variety of adhesive and sealant products for a wide range of commercial and industrial applications. Our silicone epoxy adhesives and sealants, in particular, are ideal for applications such as:
FEATURES AND USES OF ELECTRONICS SEALANTS AND ADHESIVES
Providing ultimate reliability and longevity, our electronics adhesives and sealants can be used to form bonds to many different surfaces and substrates, including:
- Ceramics
- Metals
- Glass
- Filled plastics
These specialized solutions eliminate the need for mechanical fastening and clamping while allowing for optimal ease of processing. Reliable and efficient in temperatures ranging from -45 °C to 200 °C, our electronics adhesives and sealants provide excellent dielectric insulation.
Most silicone formulations are solventless, eliminating the need for special storage, ventilation, or handling. And because many of our electronics adhesives and solvents are reworkable, they offer great flexibility and allow for easier module repair.
Electronics adhesives and sealants are frequently used in: automotive, communications, industrial, and energy industries, as well as consumer devices.
Extremely versatile, these adhesives can be used for:
- Sealing lids and housing grooves
- Cushioning or stabilizing fragile components
- Affixing components such as capacitors and coils to circuit boards
- Adhering module lids and baseplates
- Gasketing
SILICONE ADHESIVES
One of the most popular types of electronics adhesives, silicone adhesives provide excellent flexibility and high heat resistance, making them ideal for electrical, automotive, aerospace, and construction industries. There are several varieties of silicone adhesives available, including:
- Two-component systems that require a curing agent
- One-component systems that cure through air moisture
- UV or EB radiation curing adhesives
- Pressure-sensitive versions that adhere to surfaces with little pressure
RTV sealants (room-temperature vulcanizing) begin to cure as soon as they’re exposed to moisture in the air, so they must be used quickly. Pressure-sensitive sealants offer a permanent tackiness. UV- or radiation-cured sealants, on the other hand, require UV light to cure, while thermoset silicone sealants require heat to cure. Although not as strong as other sealants or adhesives, electrical silicone sealants remain flexible even when fully dried or cured. Various types of silicone sealants serve as ideal solutions for high-heat applications like engine gaskets.
In electronics fabrication, silicone adhesive sealants are often used for fixing parts on circuit boards, LCD module assembly, general sealing, and component protection. Specific formulations differ depending on intended use and can be customized to allow for enhanced thermal conductivity, superior protection of metal electrodes, and faster cure times. These sealants are available in chemical-, heat-, mildew-, and oil-resistant formulations to meet a wide range of application needs.
Industrial silicone epoxy is used for:
- General-purpose fixture sealing of tubs
- Windows, ductwork
- Gaskets
- General-purpose bonding
- Sealing
THERMAL SEALANTS
High temperatures often present problems for conventional adhesive materials and can affect printed circuit boards and assemblies. At Robert McKeown, we offer the highest-level special adhesive grades of thermal sealants, which allow for enhanced thermal conductivity. Both low-viscosity liquids and non-slump formations are available in two-cure chemistries.
We also offer one-part moisture-cure grades, which use room-temperature processing to cut back on equipment needs. After cure, the materials form strong but flexible bonds, which protect from mechanical stress and vibration. Both one- and two-part heat-cure solutions accelerate processing and support high throughput production.
Heat resistant silicone adhesives are extremely versatile materials and dispense easily at room temperature, but can also cure quickly at any thickness level at temperatures as low as 90°C. Efficacy and functionality are improved when higher temperatures accelerate cure times.
CHEMICAL RESISTANT ADHESIVES
Chemical resistant silicone adhesives are commonly used in:
- Chemical processing plants
- Chemical piping and tanks
- Medical devices
These adhesives can reliably protect against a wide range of chemicals and harsh materials, including acid, alcohol, and fuel. Depending on specific application requirements, they can also provide resistance against solvents, bases, sterilization, and water.
EPOXY BASED ADHESIVES
Epoxy based adhesives are created by mixing a resin and a hardener. Curing is initiated when the resin is mixed with a certain catalyst. The covalent bonds resulting from this combination determine the rigidity and strength of the epoxy sealant.
Epoxy adhesives can reliably adhere to a variety of materials and are ideal for applications demanding chemical resistance, high strength, and low stress. Thermally conductive, microelectronic-grade, general-purpose, high-temperature and chemical resistant epoxy adhesives are available as both one- and two-part solutions. Epoxy adhesive and sealants allow for room temperature, thermal, or UV-curing capabilities.