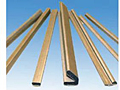
EMI Shielding Gaskets & Conductive Elastomers
Robert McKeown Co. offers electrically conductive elastomers to provide EMI/RFI shielding, as well as protection from environmental factors like dust and water. These EMI shielding gaskets add superior shielding for a range of electronic applications including aerospace, telecommunications, automotive, medical, and industrial equipment.
Caused by various external disruptive forces, electromagnetic interference (EMI) poses great risks to electronics devices, equipment, and systems of all kinds. Affecting electrical circuits through electromagnetic induction, electrostatic coupling, or conduction disturbance, EMI can result in data loss, increased error rate, total system failure, and even death.
Understanding EMI
EMI is especially dangerous in critical and sensitive applications; mass transit systems, industrial touch screens, navigation and vehicular control systems, and medical, military, and aerospace electronics are all susceptible to EMI. And depending on the specific type of electronic system, the results of EMI can be catastrophic. In medical or mass transit electronic applications, for example, EMI is not only costly and time-consuming to remedy, it’s also life-threatening. In these situations, electronics must be capable of reliable, long-lasting performance to ensure the safety and well-being of all individuals.
Having a basic understanding of EMI — specifically, the electromagnetic fields within the radio frequency spectrum that will damage your system — is key to successful, uninterrupted operations. To prevent the risks mentioned above, it’s critical to work with high-quality conductive elastomers and other EMI shielding components when designing electronic devices. EMI shielding gaskets, for instance, must be able to provide reliable sealing and protection against electromagnetic interference.
EMI Shielding Gasket Features
EMI gasket materials were once made from aluminum, copper, and steel sheets and shaped to fit electronic enclosures. However, these thin metal sheets would deform under sealing pressure, resulting in circuit leaks. EMI shielding has since evolved and is now fabricated from flexible metal screens, wires, and foams, which are not subject to the risk of deforming. One of the most effective materials for EMI shielding is a conductive elastomer, such as particle-filled silicone, which combines the electrical properties of metals with the material properties of silicone rubber.
Serving as a highly reliable sealing and insulation material, particle-filled silicone is increasingly becoming the go-to material choice for shielding gasket manufacturers. Because particles can be adapted for various durometers, they’re able to easily accommodate the specific level of hardness required by the specific gasket type. Also, these newer shielding gasket materials contain adequate amounts of metal filler to guarantee effective shielding and electrical conductivity, allowing for highly reliable, cost-effective fabrications.
Unlike the original EMI shielding gaskets, particle-filled silicone EMI gaskets are not at risk of stretching or becoming deformed, ensuring a longer lifespan. This, in turn, allows for lower maintenance costs, since replacements or repairs are needed less frequently. Tear-resistant options are also available for manufacturers working with thin-walled EMI gaskets, while adhesive-backing options allow for very simple installation.
Conductive Foam Shielding Gaskets
Conductive foam — made of polyurethane plated with copper and nickel — is also an ideal material choice for shielding gaskets. Able to withstand harsh, demanding applications, conductive foam offers great cost-efficiency and easy manufacturability. Allowing for the creation of conductive EMI gaskets — which are highly effective for shielding applications since they offer cross-section conductivity — this foam strengthens the efficacy of shielding without sacrificing any functionality.
In addition to a low compression set, allowing for long-lasting performance, conductive foam also has low flammability characteristics and high workability, and is easy to cut and slit. This versatile foam is frequently used in noise filter cores, shielded rooms, and mobile phones.
Fabric Over Foam Gaskets
At Robert McKeown Company, Inc. (RMC), we offer several lines of Parker Chomerics products, including their SOFT-SHIELD® fabric over foam (fof) EMI shielding gaskets — a low-cost, high-performance solution well-suited for commercial electronic systems.
An ideal alternative to beryllium copper or stainless steel fingerstock EMI gaskets, fabric over foam products require fewer fasteners thanks to their very low closure forces and allow for simple installation without sacrificing shielding ability. Also, cut-to-length strips of fabric over foam gaskets self-terminate, eliminating the risk of jagged edges that can cause damage and enhancing overall application reliability.
The urethane foam core has excellent compressibility, making these EMI gaskets well-suited for thin-walled plastic enclosures. Extremely versatile, fabric over foam gaskets are often used in medical and general industrial applications.
Learn More
For more information on thermal management products or to discuss how Chomerics EMI gaskets can help protect your electronics equipment, contact the team at Robert McKeown today.
/Asset/SOFT-SHIELD-3500-Low-Closure-Force-EMI-Strip-Gaskets.jpgRobert McKeown offers a variety of adhesive and sealant products for a wide range of commercial and industrial applications. Our silicone epoxy adhesives and sealants, in particular, are ideal for applications such as:
FEATURES AND USES OF ELECTRONICS SEALANTS AND ADHESIVES
Providing ultimate reliability and longevity, our electronics adhesives and sealants can be used to form bonds to many different surfaces and substrates, including:
- Ceramics
- Metals
- Glass
- Filled plastics
These specialized solutions eliminate the need for mechanical fastening and clamping while allowing for optimal ease of processing. Reliable and efficient in temperatures ranging from -45 °C to 200 °C, our electronics adhesives and sealants provide excellent dielectric insulation.
Most silicone formulations are solventless, eliminating the need for special storage, ventilation, or handling. And because many of our electronics adhesives and solvents are reworkable, they offer great flexibility and allow for easier module repair.
Electronics adhesives and sealants are frequently used in: automotive, communications, industrial, and energy industries, as well as consumer devices.
Extremely versatile, these adhesives can be used for:
- Sealing lids and housing grooves
- Cushioning or stabilizing fragile components
- Affixing components such as capacitors and coils to circuit boards
- Adhering module lids and baseplates
- Gasketing
SILICONE ADHESIVES
One of the most popular types of electronics adhesives, silicone adhesives provide excellent flexibility and high heat resistance, making them ideal for electrical, automotive, aerospace, and construction industries. There are several varieties of silicone adhesives available, including:
- Two-component systems that require a curing agent
- One-component systems that cure through air moisture
- UV or EB radiation curing adhesives
- Pressure-sensitive versions that adhere to surfaces with little pressure
RTV sealants (room-temperature vulcanizing) begin to cure as soon as they’re exposed to moisture in the air, so they must be used quickly. Pressure-sensitive sealants offer a permanent tackiness. UV- or radiation-cured sealants, on the other hand, require UV light to cure, while thermoset silicone sealants require heat to cure. Although not as strong as other sealants or adhesives, electrical silicone sealants remain flexible even when fully dried or cured. Various types of silicone sealants serve as ideal solutions for high-heat applications like engine gaskets.
In electronics fabrication, silicone adhesive sealants are often used for fixing parts on circuit boards, LCD module assembly, general sealing, and component protection. Specific formulations differ depending on intended use and can be customized to allow for enhanced thermal conductivity, superior protection of metal electrodes, and faster cure times. These sealants are available in chemical-, heat-, mildew-, and oil-resistant formulations to meet a wide range of application needs.
Industrial silicone epoxy is used for:
- General-purpose fixture sealing of tubs
- Windows, ductwork
- Gaskets
- General-purpose bonding
- Sealing
THERMAL SEALANTS
High temperatures often present problems for conventional adhesive materials and can affect printed circuit boards and assemblies. At Robert McKeown, we offer the highest-level special adhesive grades of thermal sealants, which allow for enhanced thermal conductivity. Both low-viscosity liquids and non-slump formations are available in two-cure chemistries.
We also offer one-part moisture-cure grades, which use room-temperature processing to cut back on equipment needs. After cure, the materials form strong but flexible bonds, which protect from mechanical stress and vibration. Both one- and two-part heat-cure solutions accelerate processing and support high throughput production.
Heat resistant silicone adhesives are extremely versatile materials and dispense easily at room temperature, but can also cure quickly at any thickness level at temperatures as low as 90°C. Efficacy and functionality are improved when higher temperatures accelerate cure times.
CHEMICAL RESISTANT ADHESIVES
Chemical resistant silicone adhesives are commonly used in:
- Chemical processing plants
- Chemical piping and tanks
- Medical devices
These adhesives can reliably protect against a wide range of chemicals and harsh materials, including acid, alcohol, and fuel. Depending on specific application requirements, they can also provide resistance against solvents, bases, sterilization, and water.
EPOXY BASED ADHESIVES
Epoxy based adhesives are created by mixing a resin and a hardener. Curing is initiated when the resin is mixed with a certain catalyst. The covalent bonds resulting from this combination determine the rigidity and strength of the epoxy sealant.
Epoxy adhesives can reliably adhere to a variety of materials and are ideal for applications demanding chemical resistance, high strength, and low stress. Thermally conductive, microelectronic-grade, general-purpose, high-temperature and chemical resistant epoxy adhesives are available as both one- and two-part solutions. Epoxy adhesive and sealants allow for room temperature, thermal, or UV-curing capabilities.